Components
Nextech distributes the entire RSBP portfolio of advanced components for explosion protection of industrial plants.
Below you can read more about the components we can offer:
Explosion detectors
DetEx pressure detectors detect incipient explosions within milliseconds and immediately transmit this information to the control unit. The advantages of detectors of this type are their short response time and the possibility of programming them based on current process values to provide optimal protection.
Pressure detectors are often used in explosion suppression.
LumEx optical detectors work by detecting sparks or flames and then sending a signal to the control unit to activate the associated components.
The optical detectors are often used in explosion isolation or at low Kst values and in installations in which the pressure from the explosion increases relatively slowly (protection of large volumes).
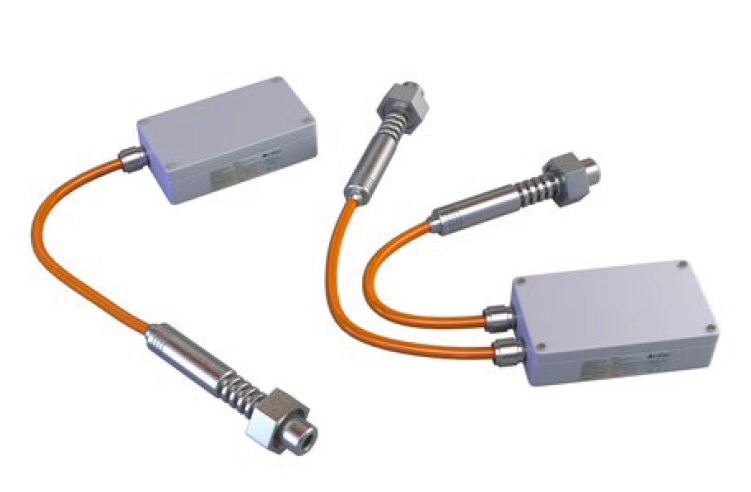
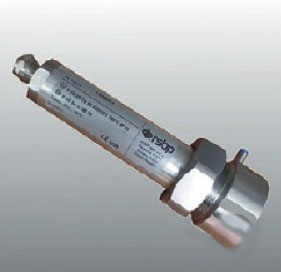
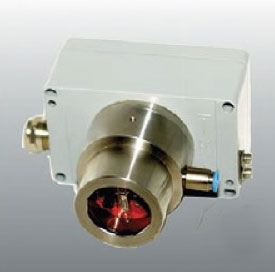
Control unit
The control unit is the “heart” of an active system. It is here where all data is processed and passed on to activate suppression or isolation of an explosion. The response time is ultra-fast, and history is backed up simultaneously, allowing the cause of system activation to be identified and clarified.
Single or multi-zone control units evaluate and archive data from the detectors, activate extinguishing or isolation of the explosion, monitor circuits for input from other devices, send data to higher-level systems, and act as a user interface for the day-to-day users of the system.
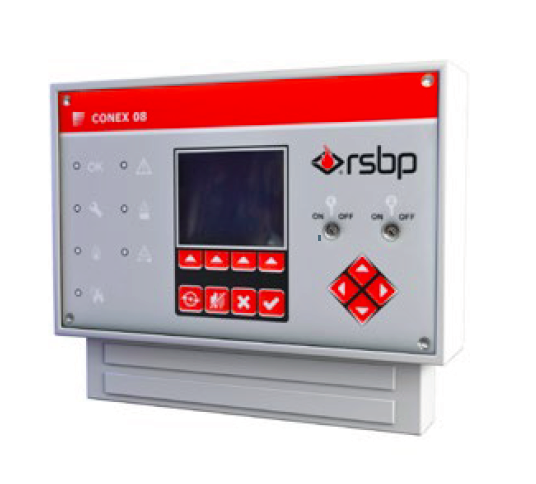
HRD containers (High-Rate Discharge)
Specially designed HRD containers contain the extinguishing agent (SBC) and are pressurised with nitrogen. When an explosion is detected, they ensure immediate and effective release of the extinguishing agent, which is distributed in the protected equipment.
Advantages of RSBP’s HRD containers:
- Range of container sizes (5, 8, 20 or 50 litres)
- Ultra-rapid explosion suppression
- Easy installation and maintenance.
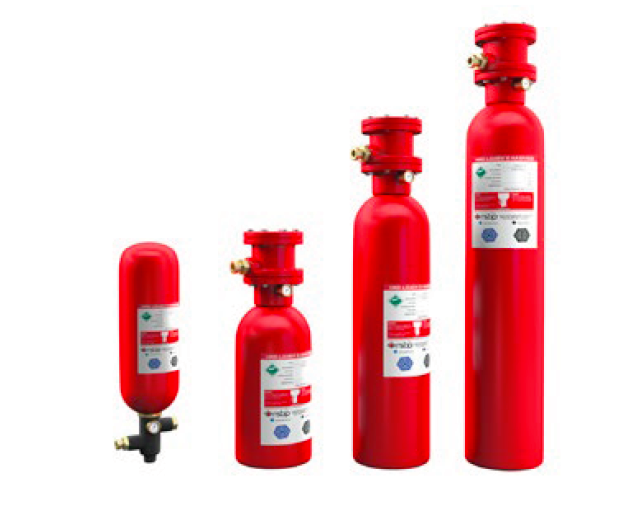
Domed, round venting panel (VMP)
A venting panel is a plate structure designed to open under known and predefined conditions, relieving pressure and flames from an explosion.
Technical advantages of the VMP panel:
- Domed three-layer venting panel with PTFE (Teflon) insulation
- For equipment with operating temperatures up to 240°C
- High vacuum support
- Available in several materials
- Suitable for cyclic operating conditions
- Certificate: EN 14 797
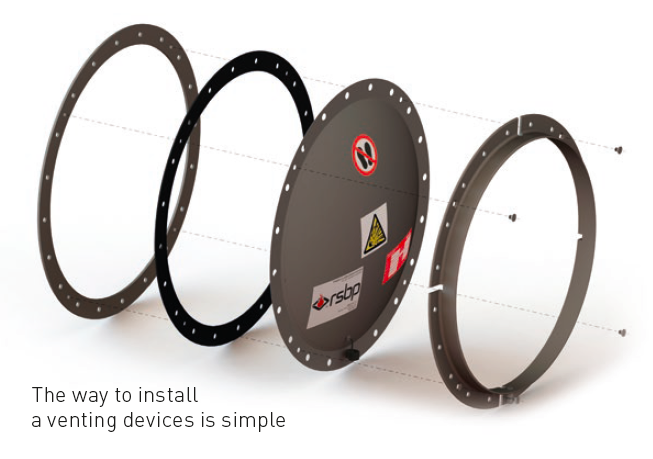
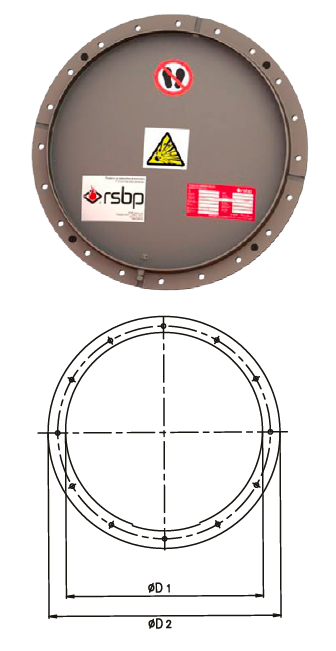
Domed, rectangular venting panel (VMP)
A venting panel is a plate structure designed to open under known and predefined conditions, relieving pressure and flames from an explosion.
Technical advantages of the VMP panel:
- Single layer design with process temperatures up to 100°C
- Three-layer design with high vacuum support and PTFE (Teflon) insulation for process temperatures up to 240°C
- Available in several materials
- Suitable for cyclic operating conditions
- Certificate: EN 14 797
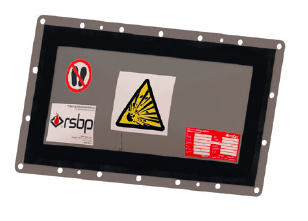
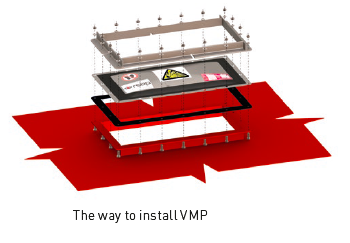
Flat, rectangular venting panel (VMP)
A venting panel is a plate structure designed to open under known and predefined conditions, relieving pressure and flames from an explosion.
Technical advantages of the VMP panel:
- For equipment with low operating pressure (up to 50% of safe opening pressure)
- For equipment with operating temperatures up to 100°C
- Possibility of frameless installation
- Stainless steel
- Economical solution
- Certificate: EN 14 797
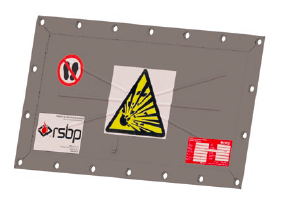
Magnetic door panels
A venting panel is a plate structure designed to open under known and predefined conditions, relieving pressure and flames from an explosion.
Technical advantages of magnetic door panels:
- For equipment with low operating pressure and without cyclic operation
- Material: Galvanised steel
- Can be used multiple times
- For equipment with very low design strength
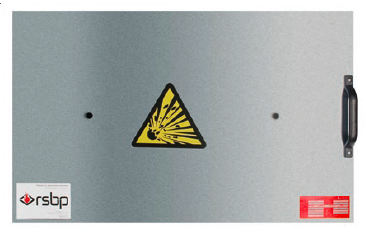
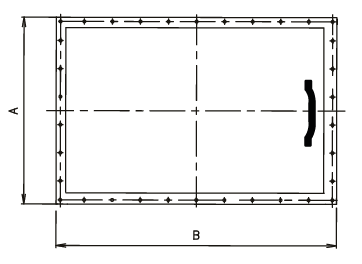
Accessories – venting panels
We offer the following options for accessories for RSBP venting panels:
- Breakage indicator for activation detection
- Option: Temperature insulation, 15 mm Armaflex
- Option: Frames for mounting both round and square panels
- Option: Wide range of gaskets for sanitary requirements, high temperatures etc.
FLEX flameless explosion venting
Flameless explosion venting is used when it is not appropriate to vent via conventional venting panels. The design allows the explosion to vent both pressure and flame, but without immediate impact on the surrounding environment. Thus, the panels can be used indoors and in areas with special risk conditions, including walkways where people may move.
Explosions can reach temperatures of up to 1500°C. During explosion venting, the temperature is lowered to a level that does not endanger the surrounding production machinery or the company’s employees.
Application:
The typical application is for indoor venting where flame and pressure are not allowed to move freely.
Flameless explosion venting – also called flame killers – is used on components such as filters, bucket elevators, cyclones and spray dryers, and often in combination with other isolation equipment to ensure that the explosion does not spread to other connected equipment.
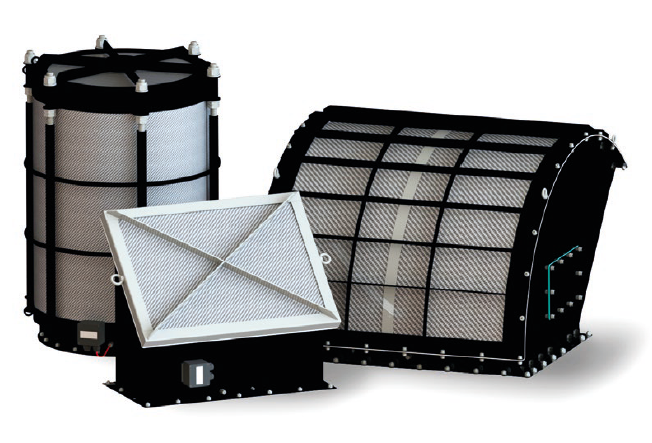
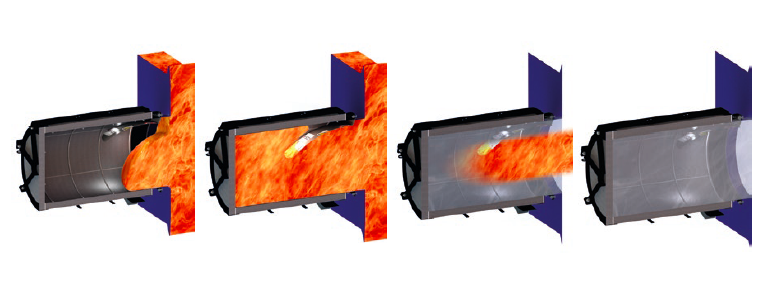
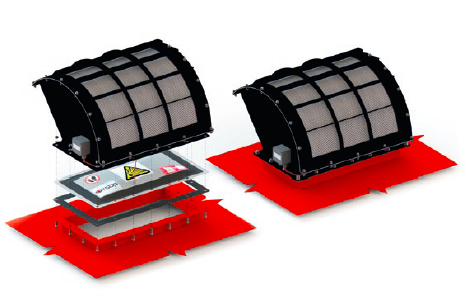
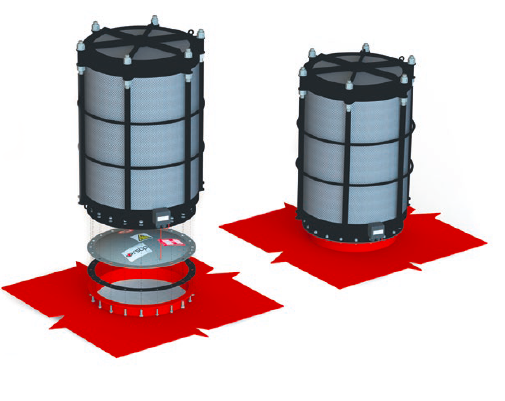
Back pressure valve B-FLAP – Mechanical isolation
B-FLAP I is a mechanical flap designed to prevent the spread of flames and pressure between parts of production equipment during an explosion.
Advantages of the B-FLAP back pressure valve:
- Wide range of sizes DN 100 to DN 800
- Mechanical component that does not require electrical energy or an activation system
- Low pressure drop
- High compressive strength
- Available option: Position indicator
- Available option: Dirt indicator on the flap coupling surface
- Easy installation, inspection and maintenance
- Low maintenance costs
- Mechanical isolation when the flap closes
- Can be used for processing with light metal dust
- Possibility of coupling with RPD component (Reducer of Pressure Drop)
How B-FLAP I works:
In normal operation, the back pressure flap is held open by the air flow inside the pipe, or it is held open by the RPD mechanism, which holds the flap open independently of the air flow. This solution significantly minimises pressure loss in the pipe system.
In the event of an explosion, the back pressure flap is closed and locked, preventing the explosion from spreading to other parts of the equipment and the production machinery.
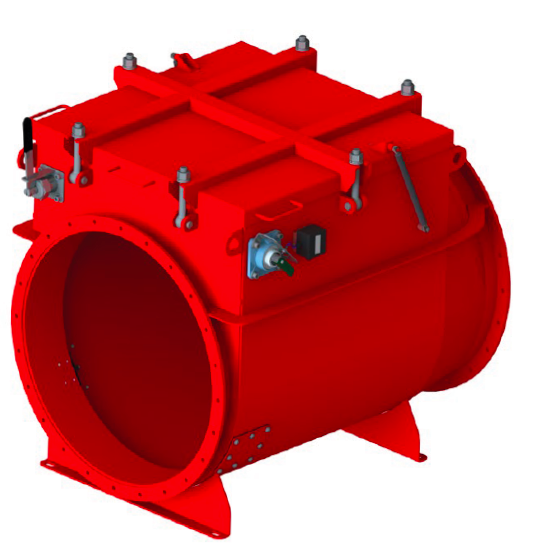
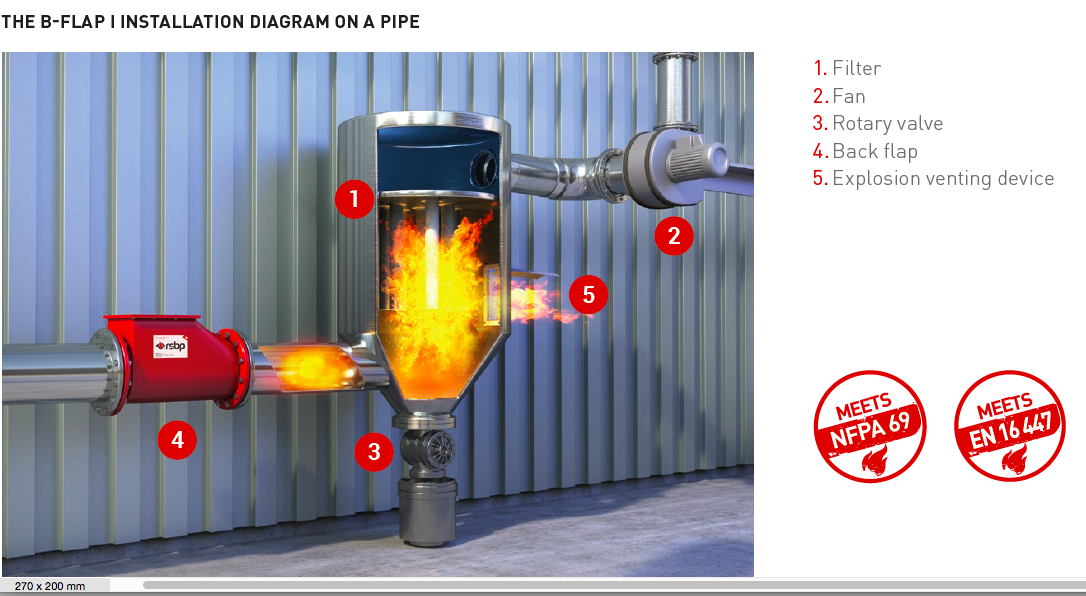
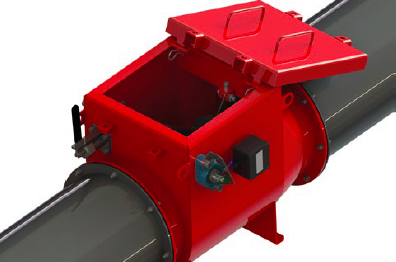
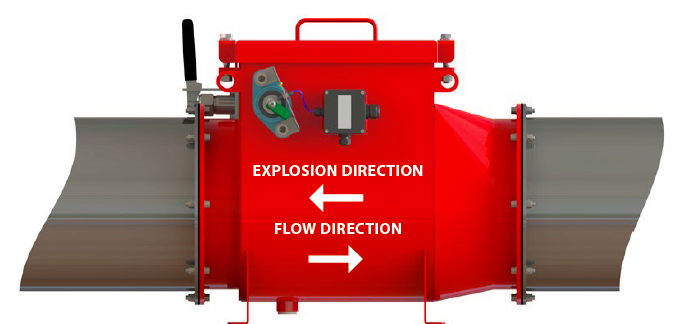
Quick-acting slide valve GATEX
The GatEx quick-acting slide valve is used for complete closure of a pipe in the event of an explosion. It is therefore particularly useful for protecting production machinery where there is a risk of dust explosions. The system can be used for pneumatic transport lines, extraction systems and systems designed for maximum explosion pressure (pmax).
Advantages of the slide valve:
- For pipe sizes from DN 50
- Pressure up to 17 bar
- Ultra-fast response time
- Short installation distance
How the quick-acting slide valve works:
The GatEx quick-acting slide valve is actuated when an imminent explosion is detected. A detector sends a signal about the emerging explosion to a control unit, which then activates a closing mechanism on the valve. The slide valve is closed pneumatically. It uses a fail-safe design that places the slide valve in a safe state if its functionality cannot be guaranteed (e.g. if the power supply or communication system is interrupted or the pressure drops).
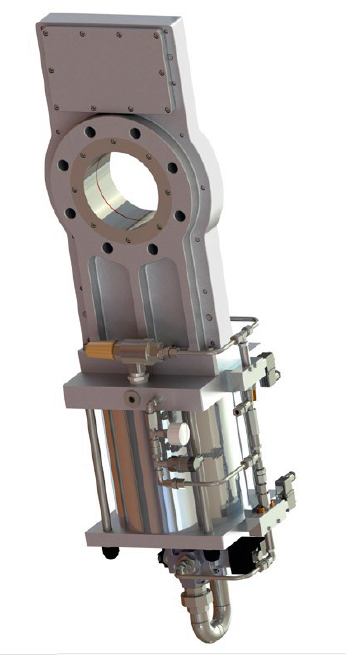
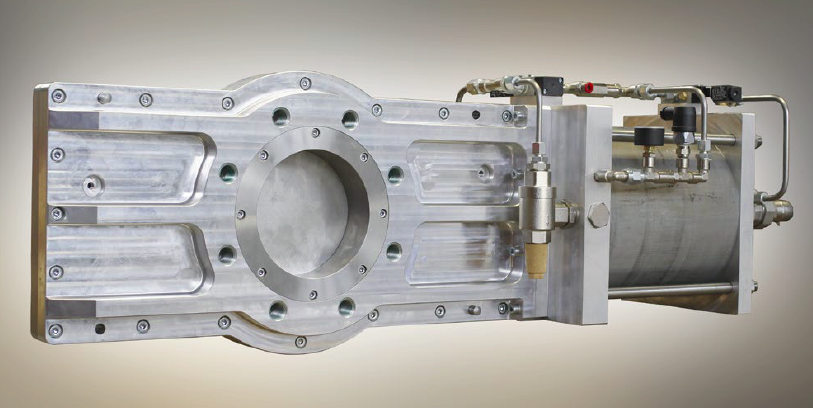
Quick-closing valve
The quick-closing valve prevents the spread of flames and pressure from an explosion to other parts of the production system. The valve is used for the protection of pipe-based transport systems.
Advantages of quick-closing valve:
- Can be used for pipe sizes from DN 100
- Can be used for equipment with operating temperatures up to 250°C
- Does not require power supply or activation system
- Low actuation pressure and pressure drop
- Short installation distance
- Easy maintenance
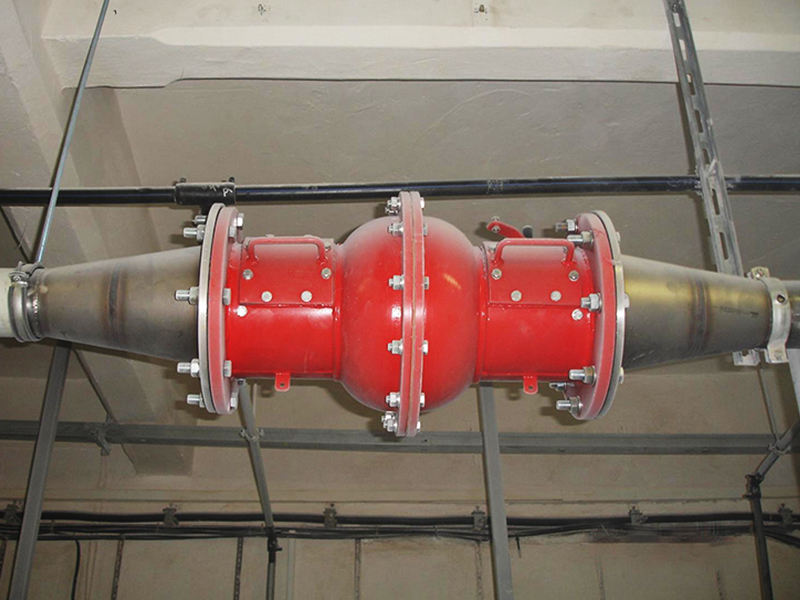
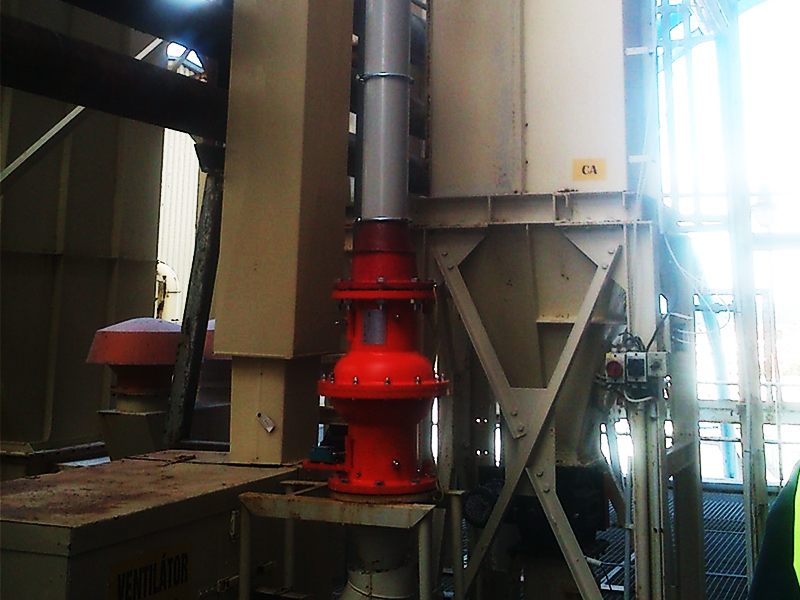
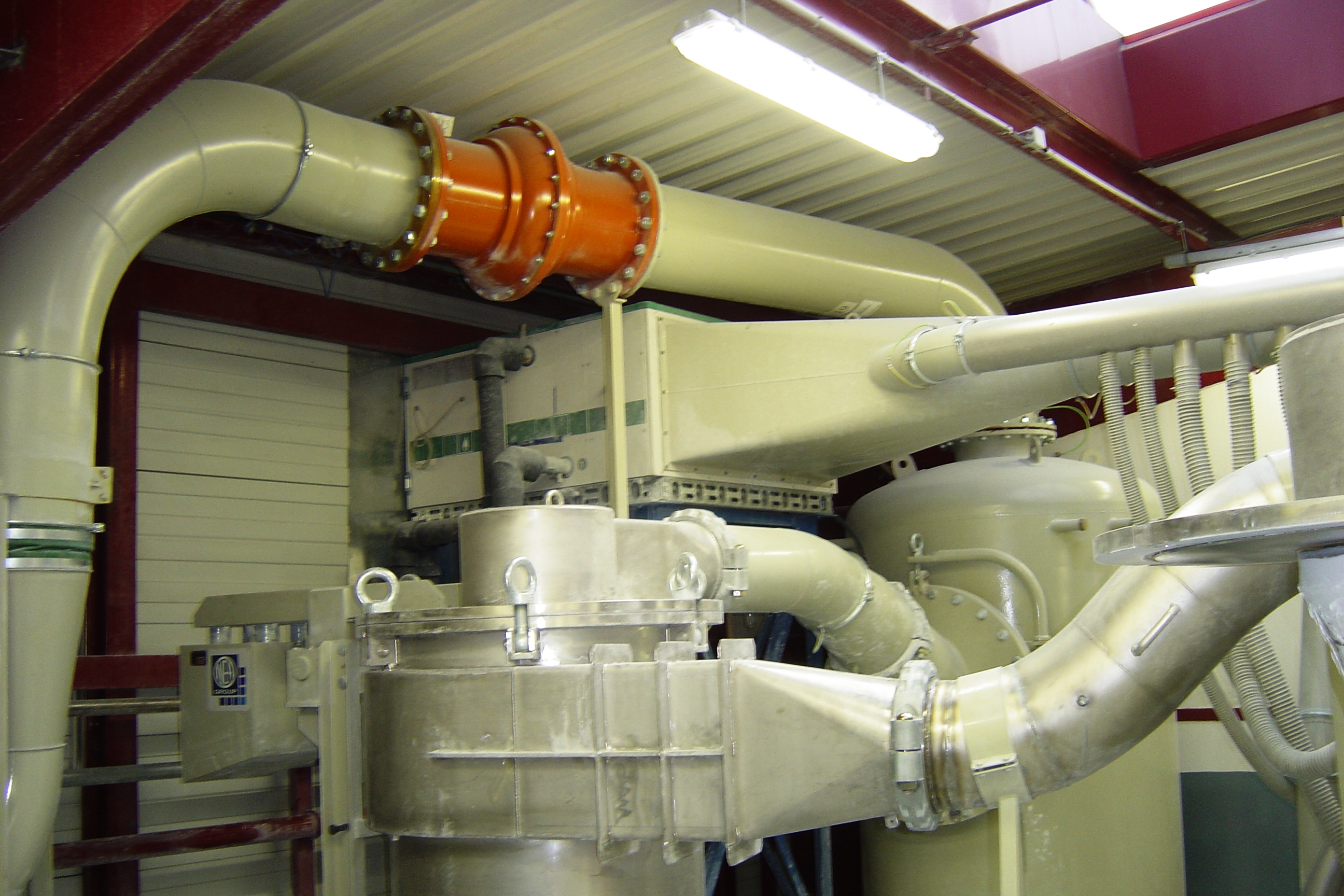
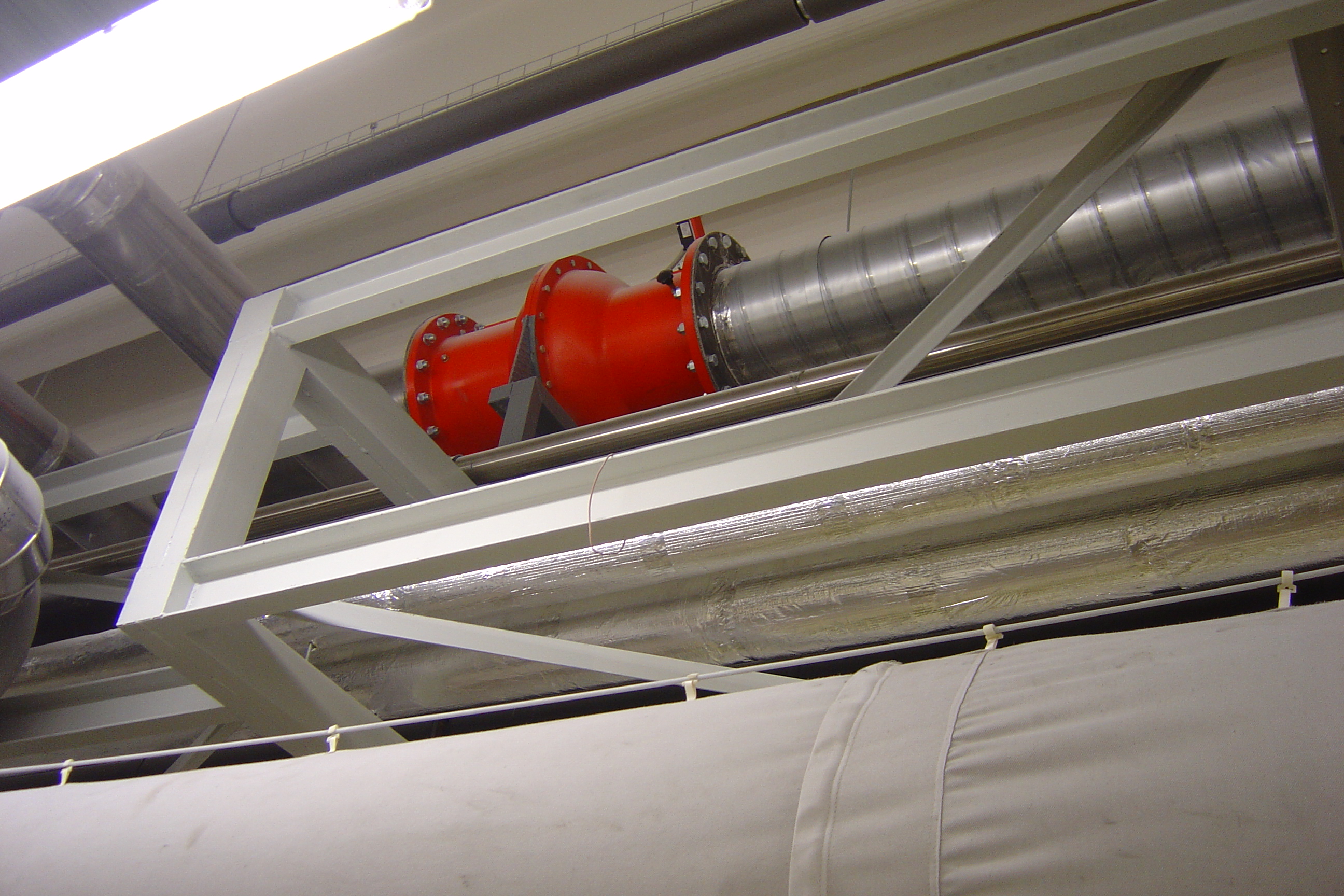
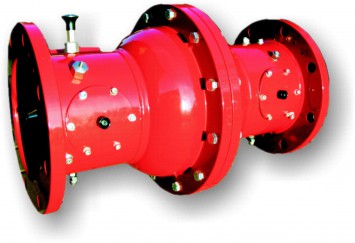
Explosion diverters
In 2020, we have had to discontinue explosion diverters from our range, as the product does not provide sufficient protection compared to the other protection concepts available. EN 16020:2011 also states that there is no particularly high level of assurance of the effectiveness of the technology.
An explosion diverter works in normal operation like any other part of a pipeline, but in the event of an explosion it switches on and diverts the explosion into a safety zone.
Explosion diverters are typically used together with filters to ensure that the explosion does not propagate back into production areas or other connected equipment, with the risk of secondary explosions.
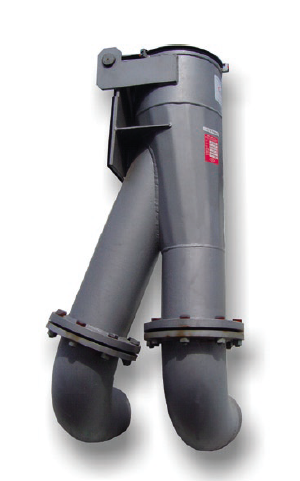
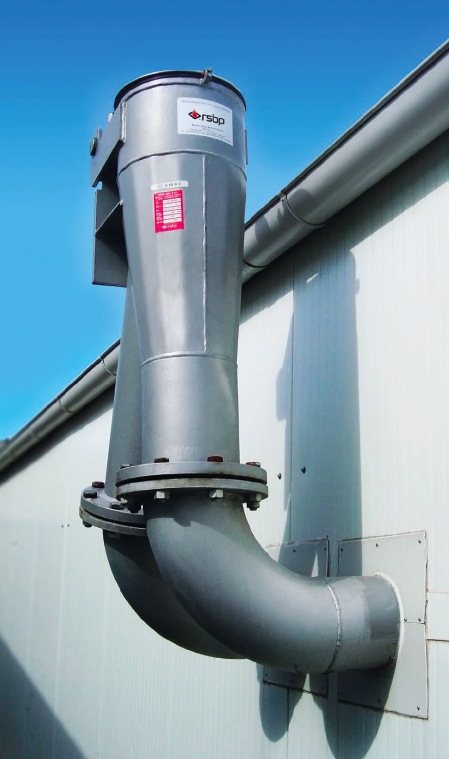
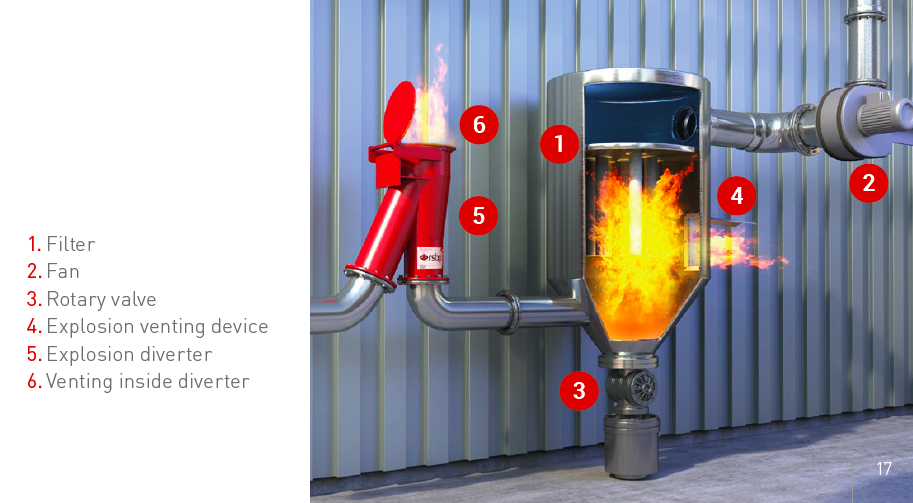