Systems
Nextech offers a wide range of solutions for effective explosion protection, so we can always put together a system that provides maximum safety in the production equipment in question.
EXPLOSION SUPPRESSION VIA CHEMICAL SUBSTANCES – HRD SYSTEM
RSBP’s HRD (High Rate Discharge) system is a highly reliable, thoroughly tested and approved explosion suppression system. It detects the explosion in the start-up phase and then suppresses dust explosions within milliseconds. This limits the pressure development so that it is kept below the design strength of the system in question. Machine damage is prevented and the risk of the much more dangerous secondary explosions is minimised.
Thus, the HRD system not only protects against material damage, but – most importantly – also provides effective protection for the company’s employees.
How the HRD system works:
Highly sensitive detectors can detect the onset of an explosion within milliseconds, causing the system to open the HRD valves and activate HRD containers with extinguishing agent. The pressure of the extinguishing agent then activates specially designed telescopic nozzles, which ensure efficient distribution of the extinguishing agent throughout the protected area. Explosion suppression activation is very fast and ensures that the pressure from the explosion is quickly under control, eliminating unwanted consequences such as injury to workers or damage to machinery.
Advantages of the HRD system:
- Tested and effective technology
- Fast response time
- High operational reliability
- Can be used indoors and outdoors
- Suitable for toxic and hazardous materials
- Separate storage of detector data
- Can be tailored to customers’ quality requirements
- Flexible use of components
- Easy and quick replacement of components after activation
- Extinguishing agent suitable for the food industry
See how the system works in the video below:
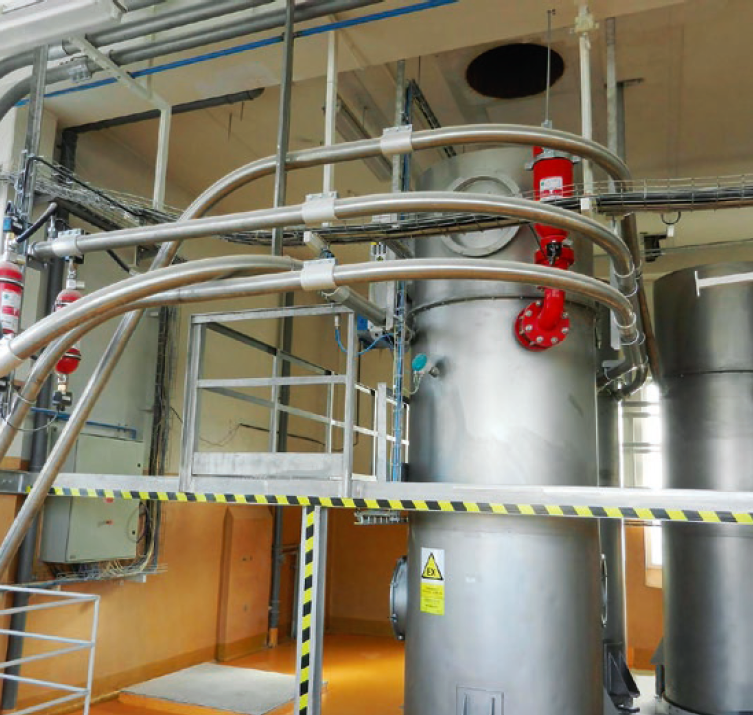
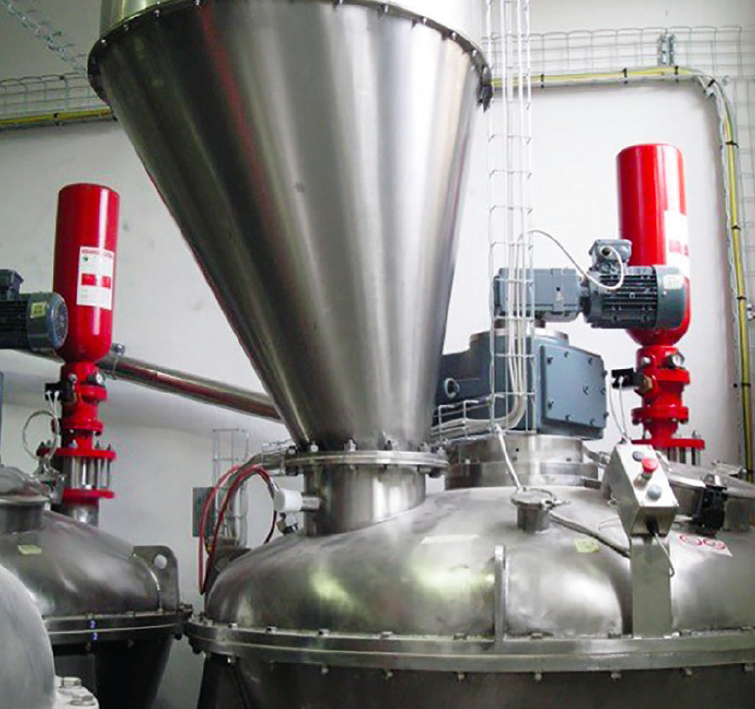
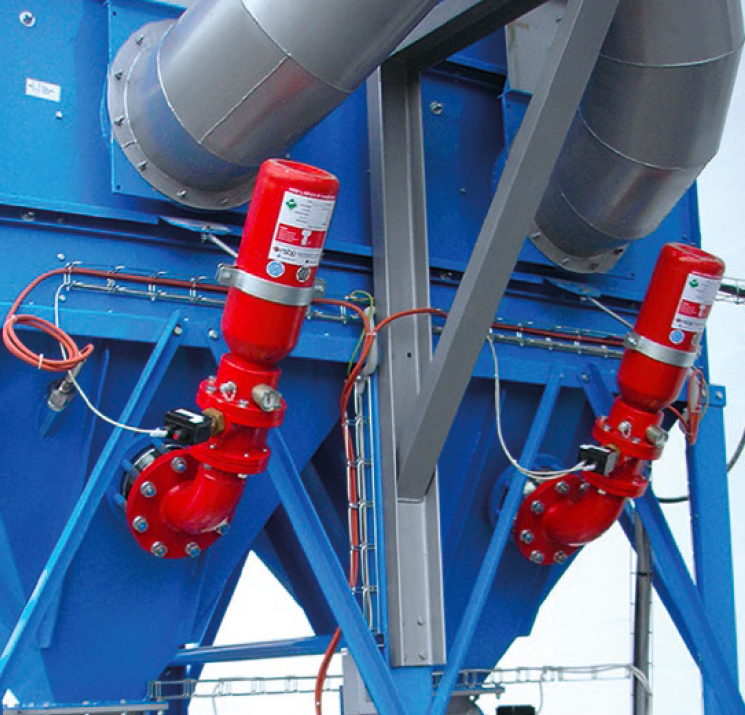
WATER SHOT – EXPLOSION SUPPRESSION VIA WATER
In systems where chemical suppression cannot be used, we offer what is known as the Water Shot. This is a special HRD system that has a configuration very similar to chemical suppression, but where the suppression containers are specially designed for water suppression. Water Shot is designed to protect against explosions, especially in the food industry, where powder extinguishing is not an option. The system specifically targets elements of the production system in which water is already used as a cleaning agent.
Advantages of Water Shot:
- Production is not contaminated with suppression powder.
- After the suppression system has been discharged, simply wipe the machine parts dry; it is not necessary to rinse off the extinguishing agent.
- Water Shot is an environmentally-friendly extinguishing agent.
- Water Shot is easy and inexpensive to refill after discharge.
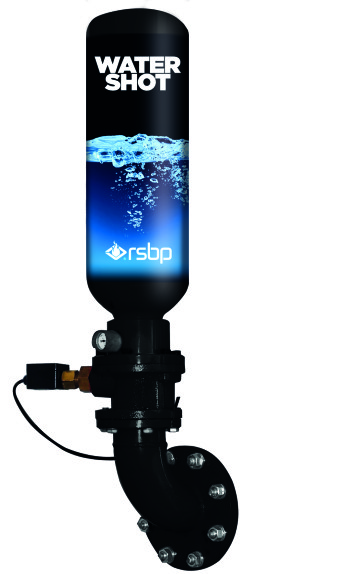
Explosion venting
Explosion venting equipment is panel-based protective equipment that provides targeted protection for industrial production machinery where there is a risk of explosion.
RSBP’s venting equipment minimises the risk of explosions and prevents the losses, injuries and damage that an explosion can cause. RSBP’s venting equipment is thus an effective and economical solution for protection against damage from dust explosions.
Explosion venting benefits:
- Highly effective and reliable
- Long service life
- Resistance to wear, impact and weather conditions
- Simple installation and replacement, and easy access to spare parts
- Can be produced to desired opening pressure
- Wide range of panel sizes and accessories
- Explosion venting is the most economical safety solution
How explosion venting works:
A venting panel is a plate structure designed to open under known and predefined conditions.
During normal operation, the venting opening of the equipment is covered by the venting panel. If the pressure is exceeded inside the equipment, the venting panel opens, relieving pressure away from the exposed machinery.
The venting capacity must be calculated in order to ensure it is correct. Thus, we need to know the volume of the equipment, the explosion values of the product, whether it is possible to discharge directly to the open air or whether a channel must be connected to divert the explosion, etc. Once these parameters are defined, the venting opening and panel can be designed so that the venting installation provides optimum safety for workers and machinery under the given conditions.
See how the system works in the video below:
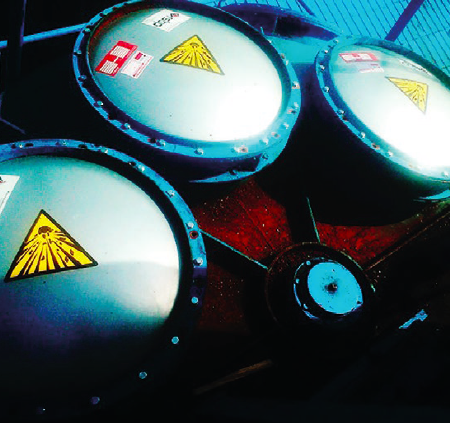
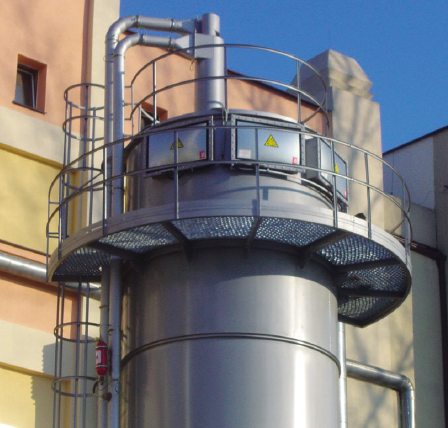
eksplosionspanel
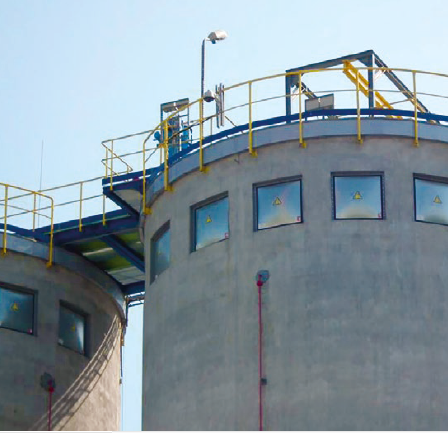
eksplosionsmembran
Flameless explosion venting
Flameless explosion venting enables safe explosion venting in enclosed or indoor areas without release of flames, pressure and heat to the surrounding environment. The system can thus be used for machinery and equipment located in areas that are difficult to access, without the need for rebuilding or adapting building components, which typically has to be done when using classic types of explosion venting.
Advantages of flameless explosion venting:
- Effective stopping of flames and heat
- Provides a safety zone for equipment, buildings and employees
- Effective dust collection – no contamination of the machine or the environment
- Can be used in the food and pharmaceutical industries
- Highly effective and reliable
- Simple installation and maintenance-free operation
- No costs for modification of buildings
- Economical solution
- Can be used for machines that use melting, coarse dust as well as fine metal dust.
See how the system works in the video below:
Explosion isolation via valves and dampers
Mechanical explosion isolation ensures that flames, heat and pressure from an explosion do not spread to other parts of the plant – both inside the production system and outside, where there is a risk of injury to company employees and damage to other connected production equipment.
Our explosion isolation solutions can be used, for example, in transport systems, extraction systems and other types of pipe systems in production plants where there is a risk of e.g. dust explosions or gas explosions.
See how the isolation systems work in the videos below:
B-flap:
Gatex:
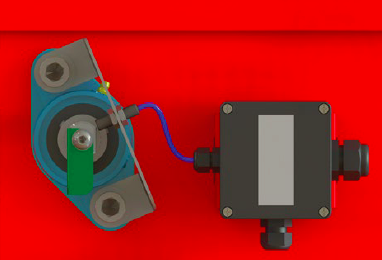
rico
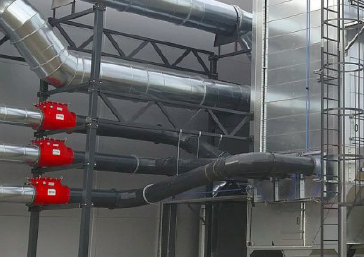
kontraklap
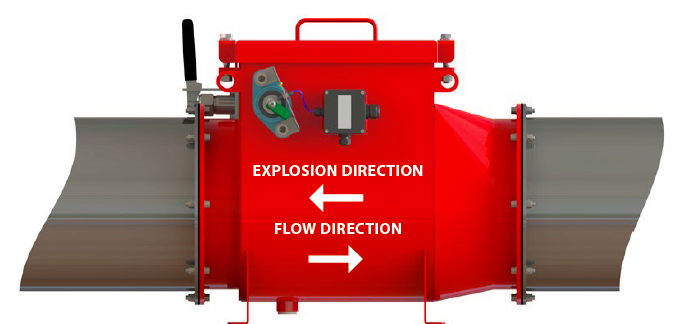
Chemical explosion isolation
Chemical explosion isolation works by using sensitive detectors to transmit data about an emerging explosion to a control unit, which immediately activates the release of an extinguishing agent that forms a barrier in pipe systems around the machine part where the explosion has occurred.
This isolates the flame front, while allowing the pressure wave to pass freely, resulting in reduced pressure build-up at the site of the explosion. This effectively prevents machinery damage and worker injury.
See how the system works in the video below:
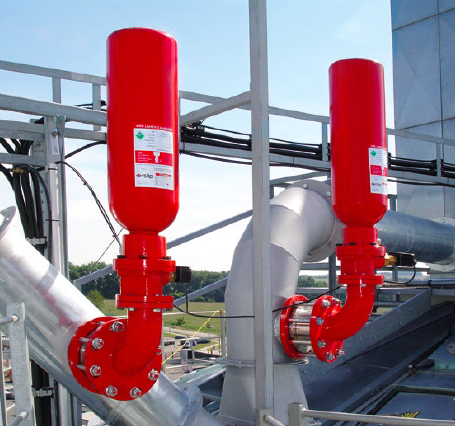
Elevex – Explosion protection for bucket elevators
ELEVEX is an effective solution for explosion protection of vertical bulk material transport.
The system significantly reduces explosion pressures, thus preventing serious machinery damage and worker injury.
The list of potential ignition sources that can cause explosions in bucket elevators or similar vertical transport systems is long, and the probability that an explosion will occur when the system is in operation is high. Use of the ELEVEX system will not prevent the ignition of an explosion in a bucket elevator, but the damage from the explosion can be reduced to an absolute minimum.
The ELEVEX system includes explosion protection for both interior and exterior systems. Each solution is tailored to the individual customer's needs and can, for example, be composed of explosion suppression, explosion venting and flameproof explosion venting components.
Advantages of ELEVEX explosion protection for bucket elevators:
- Tested and approved explosion protection system
- High-quality components
- Easy installation on existing transport systems
- Maximum protection for minimum cost
- Can also be used for high elevators
See how the system works in the video below:
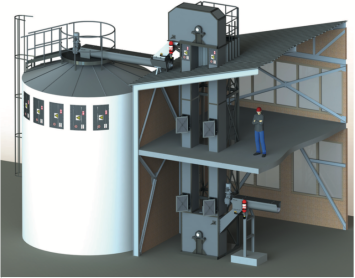
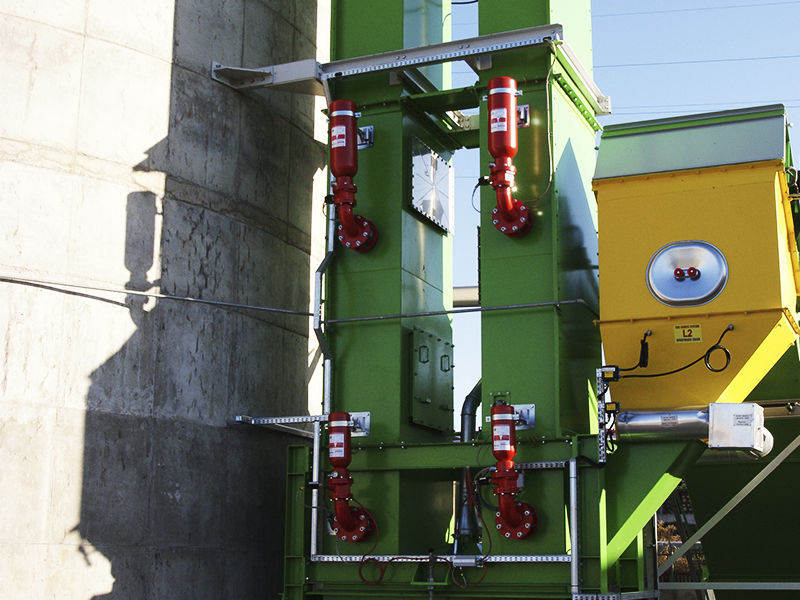